Although today’s rocket engines are advanced and powerful, they tend to rely on traditional — and naturally volatile — fuels like hydrazine or liquid oxygen and kerosene. Firehawk Aerospace has a safer and more stable new fuel, new engines, and millions in new funding to take it through the next round of tests to its first launch.
Firehawk appeared on the scene two years ago with a fresh take on hybrid engines — those that use a fuel with both solid and liquid qualities. The breakthrough made by CEO Will Edwards and chief scientist Ron Jones was to give that fuel a structure and 3D print it in a specially engineered matrix.
The structured, semisolid fuel is more stable and easier to transport than other fuels, and burns in a very predictable way. The company designed engines around this concept and tested them at smaller scales, but recently graduated to the kind of engine you might actually use if you were going to space.
“It’s a unique engine with its throttling ability, low cost of manufacture, and a parametric design, so we can design for a missile interception system or second stage booster,” said Edwards.
The company recently performed full engine burn tests at Stennis Space Center with NASA supervision, and they’re ready to fly — the last step before reaching a technology readiness level that would permit the company to step up its revenue.
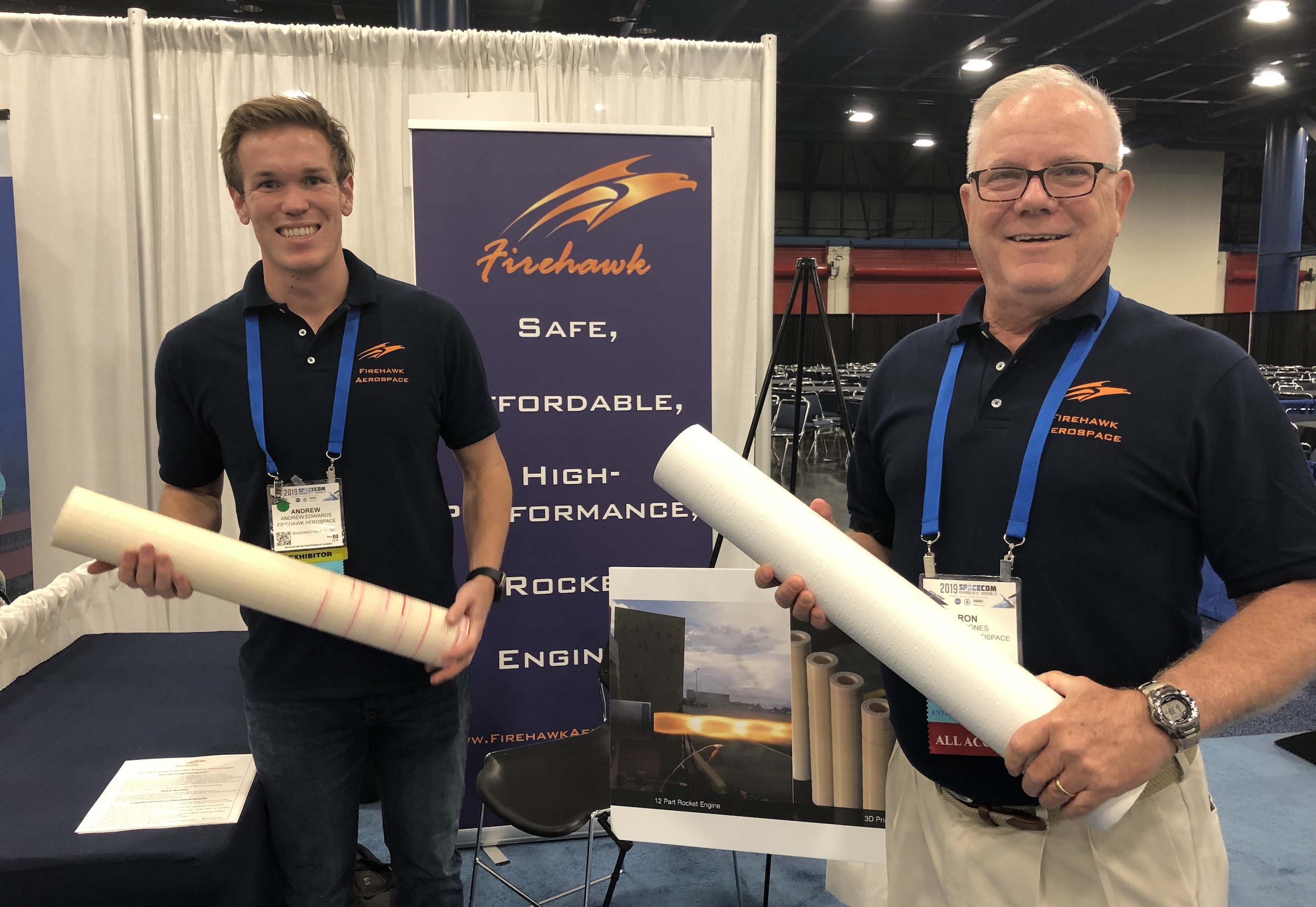
Firehawk CEO Will Edwards (left) and chief scientist Ron Jones hold 3D-printed fuel tubes Image Credits: Firehawk Aerospace
In addition to better safety, printing the fuel grains differently makes it possible to create different thrust characteristics. And the whole thing can be safely slowed, stopped and started again multiple times — not something you see often in a launch vehicle rocket engine. Normally once you fire those up, they blast at 100% until they run out of fuel, meaning you only get one shot at it and your options for force vectors are limited — more like a drag racer than a normal car.
“Our engine can replace solid rocket motors with something significantly lower cost, on par with fuel performance, but you can control its burn — that’s something the industry finds incredibly compelling,” Edwards noted.
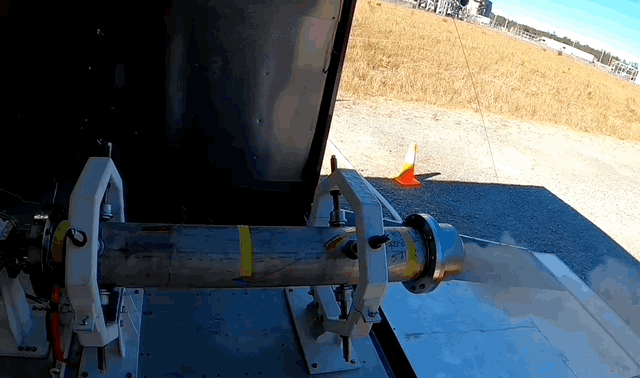
A Firehawk engine being tested at Stennis Image Credits: Firehawk Aerospace
Not in the sense of first-stage launch vehicle engines, for which that high-thrust, full-throttle fire is desirable, but for systems where a little more complexity would be welcomed: second-stage thrust (e.g., boosting payloads to a certain orbit once they’re out of the atmosphere) and missile interception systems, for which precision is paramount.
Edwards also suggested in-space propulsion like satellite maneuvering as a potential application, since due to the volatility of fuels, more low-impulse methods like ion engines are often used. Firehawk’s fuel is “inert by nature,” making it a lot less of a liability in, for example, a multipayload launch. Would you want your satellite stored next to a barrel of kerosene?
The new Series B funding round will enable more tests, more R&D, and the production of more engines to meet demand — though predictably with a company working with the likes of Raytheon, NDAs prevent the nature of that demand to be described with any specificity. They’ve raised $15.5 million so far but are expecting to close at $17 million shortly.
The list of funders is a bit long, but for the record: Star Castle VC led the round, with participation from Raytheon, Draper & Associates, Goff Capital, Cathexis Ventures, Plains VC, Victorum Capital, Stellar VC, Capital Factory, Echo Investments, and Hemisphere Ventures.
Although the engines currently being tested are nearly ready for use by customers, Edwards stressed that this is just the start. New applications are potentially just a few keystrokes away:
“We can create really unique fuel grain geometries, and by changing the design we can improve its performance. It’s just a matter of rewriting some code and uploading that to our 3D printers,” he said, adding that the new funding has let them buy and customize their own printers, CNC machines, and test setups for deployment in a new Addison, Texas, location. “We’ll be able to move through our next test campaign much more quickly.”
Here’s the happy team at the new HQ:
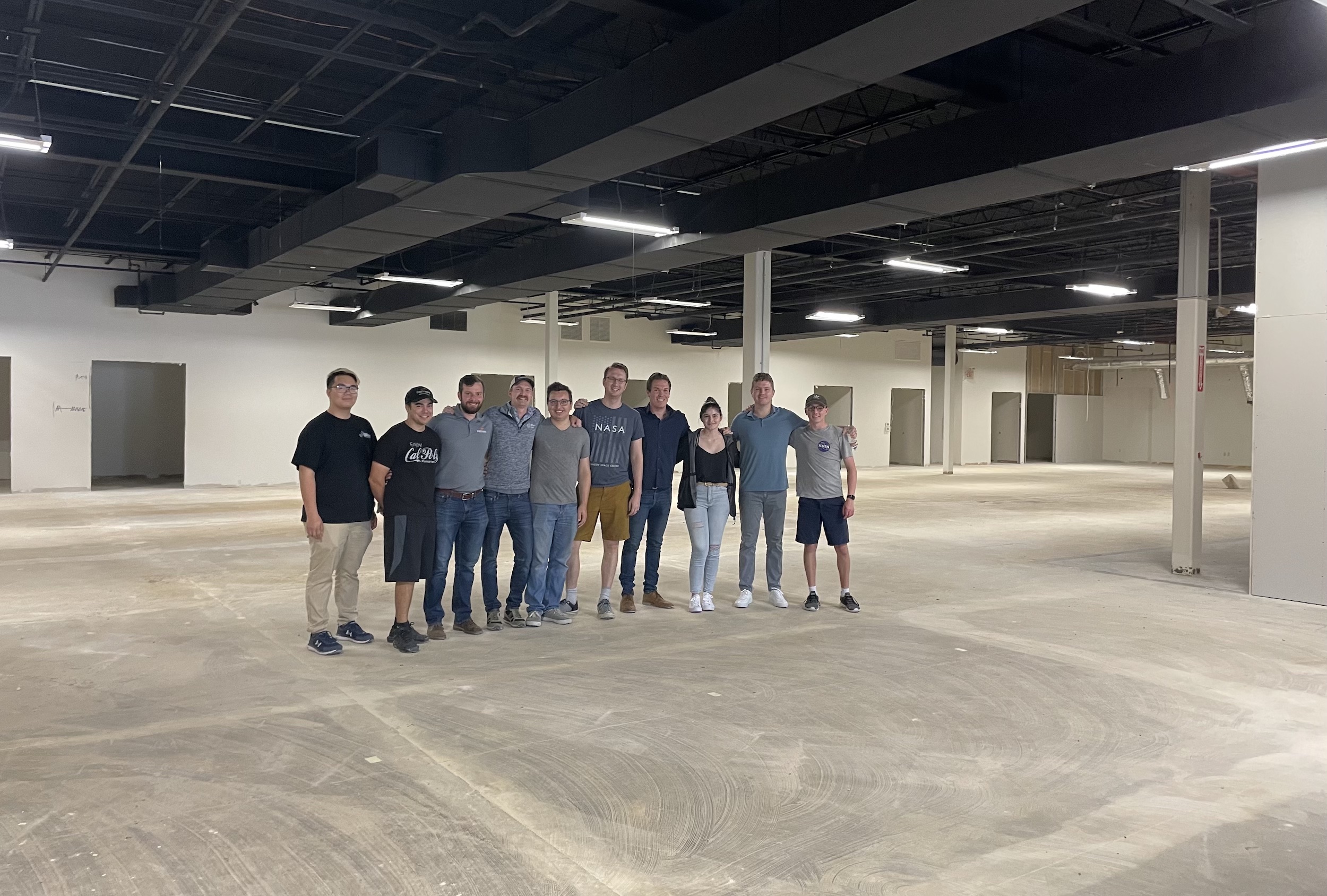
Image Credits: Firehawk Aerospace
More tests should be coming next month, which should clear the way for a launch of some kind in the near (but still unspecified) future.
Firehawk’s rocket engines and 3D-printed fuel hit testing milestones ahead of first launch by Devin Coldewey originally published on TechCrunch